Unraveling the Mystery of Porosity in Welding: Tips for Lessening Defects and Making The Most Of Quality
In the complex globe of welding, porosity continues to be a persistent obstacle that can significantly affect the high quality and stability of bonded joints. As we dig right into the midsts of porosity in welding, discovering the tricks to its avoidance and control will certainly be extremely important for experts looking for to understand the art of high-quality weldments.
Understanding Porosity in Welding
Porosity in welding, a common concern encountered by welders, describes the visibility of gas pockets or voids in the bonded product, which can jeopardize the stability and high quality of the weld. These gas pockets are typically trapped throughout the welding procedure as a result of numerous aspects such as incorrect protecting gas, contaminated base materials, or inaccurate welding specifications. The development of porosity can compromise the weld, making it vulnerable to cracking and rust, eventually leading to structural failings.
By identifying the significance of keeping correct gas protecting, making sure the sanitation of base materials, and optimizing welding setups, welders can significantly minimize the chance of porosity formation. On the whole, an extensive understanding of porosity in welding is crucial for welders to produce top quality and resilient welds.
Common Reasons of Porosity
When evaluating welding processes for potential quality issues, understanding the common causes of porosity is important for preserving weld integrity and avoiding structural failures. Porosity, characterized by the presence of dental caries or gaps in the weld metal, can dramatically endanger the mechanical buildings of a bonded joint.
Furthermore, welding at improper criteria, such as exceedingly high travel rates or currents, can generate too much disturbance in the weld swimming pool, trapping gases and creating porosity. By dealing with these common reasons through correct gas protecting, product preparation, and adherence to optimum welding parameters, welders can reduce porosity and enhance the top quality of their welds.
Strategies for Porosity Avoidance
Applying effective precautionary steps is crucial in lessening the event of porosity in welding procedures. One method for porosity avoidance is guaranteeing appropriate cleaning of the base steel before welding. Impurities such as oil, grease, corrosion, and paint can lead to porosity, so complete cleaning utilizing ideal solvents or mechanical techniques is essential.

Utilizing top quality filler materials and shielding gases that are suitable for the base steel and welding procedure can dramatically reduce the risk of porosity. In addition, maintaining appropriate welding specifications, such as voltage, present, travel speed, and gas flow rate, is vital for porosity prevention.
Furthermore, using correct welding strategies, such as preserving a constant travel speed, electrode angle, and arc size, can aid protect against porosity (What is Porosity). Adequate training of welders to ensure they adhere to ideal methods and quality assurance procedures is dig this likewise vital in lessening porosity problems in welding

Ideal Practices for Top Quality Welds
Making sure adherence to market standards and correct weld joint preparation are essential facets of attaining regularly premium welds. Along with these fundamental steps, Check Out Your URL there are several ideal methods that welders can execute to even more enhance the top quality of their welds. One secret practice is keeping correct tidiness in the welding location. Pollutants such as oil, grease, corrosion, and paint can adversely affect the top quality of the weld, resulting in defects. Extensively cleaning the work surface and surrounding location before welding can help minimize these problems.
An additional best technique is to meticulously choose the appropriate welding criteria for the certain products being joined. This consists of establishing the appropriate voltage, existing, travel speed, and securing gas flow rate. Correct specification choice makes certain optimal weld infiltration, blend, and overall high quality. In addition, using top notch welding consumables, such as electrodes and filler metals, can considerably affect the last weld quality. Investing in premium consumables can lead to more powerful, extra durable welds with fewer problems. By complying with these ideal techniques, welders can consistently produce premium welds that fulfill sector criteria and go beyond consumer assumptions.
Significance of Porosity Control
Porosity control plays an important function in guaranteeing the integrity and quality of welding joints. Porosity, defined by the existence of dental caries or gaps within the weld steel, can substantially jeopardize the mechanical properties and structural integrity of the weld. Excessive porosity damages the weld, making it a lot more vulnerable to breaking, rust, and total failure under functional loads.
Efficient porosity control is important for keeping the desired mechanical properties, such as stamina, ductility, and toughness, of the welded joint. What is Porosity. By decreasing porosity, welders can improve the total quality and integrity of the weld, ensuring that it satisfies the efficiency requirements of the desired application
Furthermore, porosity control is crucial for attaining the desired visual look of the weld. Excessive porosity not only damages the weld but likewise diminishes its visual charm, which can be important in industries where looks are essential. Appropriate porosity control strategies, such as making use of the correct shielding gas, controlling the welding parameters, and making certain proper cleanliness of the base materials, are important for creating high-quality welds with minimal problems.
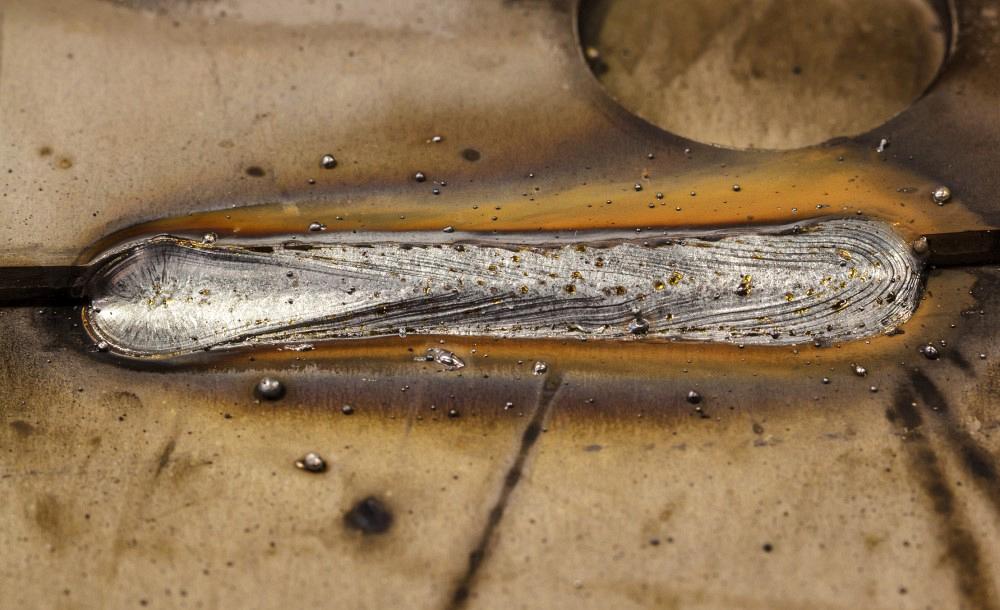
Verdict
Finally, porosity in welding is a typical flaw that can endanger the top quality of the weld. By understanding the reasons for porosity and applying correct avoidance techniques, welders can reduce problems and see accomplish better welds. It is crucial to regulate porosity in welding to ensure the integrity and strength of the final product. Implementing finest techniques for porosity control is critical for achieving optimum welding outcomes.